Linear actuators come in different forms, with pneumatic and electric being the most common when high forces from hydraulic systems aren't required. Here are 15 factors to consider.
What is an actuator?
According to Wikipedia, an actuator is a component that moves or controls a mechanism. A linear actuator either pushes with force or carries a load linearly to specific positions. While similar in structure, their differences start with the power source—hydraulic (fluid), pneumatic (air), or electric (AC/DC).
Â
Choosing the right linear actuator depends on how well it meets your application requirements, such as load, speed, accuracy, etc.
Â
For instance, pneumatic actuators can offer higher speeds, but electric actuators provide more precise control since air and fluid pressure are harder to manage than electricity.
For average loads that don’t require the high forces of hydraulic actuators, the choice is between a pneumatic or electric actuator. In this post, we’ll compare the pros and cons of both to help you decide for your next project.
Â
Here are 15 key factors to consider when choosing between pneumatic and electric actuators.
 |
Pneumatic Actuators |
Electric Actuators |
Design |
Simple |
Complex |
Force |
Depends on air pressure |
Depends on screw pitch/lead |
Speed |
High |
Low |
Accuracy |
Low |
High |
Repeatability |
Low |
High |
Motion Control Capability |
Low |
High |
Efficiency |
Low |
High |
Cost |
Lower initial cost |
Lower total cost of ownership |
Data Collection |
Still developing |
Highly developed |
Environment |
Harsh, hazardous |
Refer to IP rating |
Temperature |
Higher ambient temperature |
Lower ambient temperature |
Noise |
High |
Low |
Maintenance |
High |
Minimal |
Life |
Estimated |
Calculated |
Ideal Application |
End-to-end positioning |
Multi-point positioning |
Please read on for more information.
Â
Design
Pneumatic actuators are simpler in design compared to electric actuators, which use more complex components like ball screws and electric motors. The simple design of a pneumatic actuator is also more compact, but when considering all necessary components for maintaining air pressure, it might actually take up more space.
Here we compare a typical pneumatic actuator with an electric cylinder using a ball screw.
Pneumatic Actuator |
Electric Actuator with a Ball Screw |
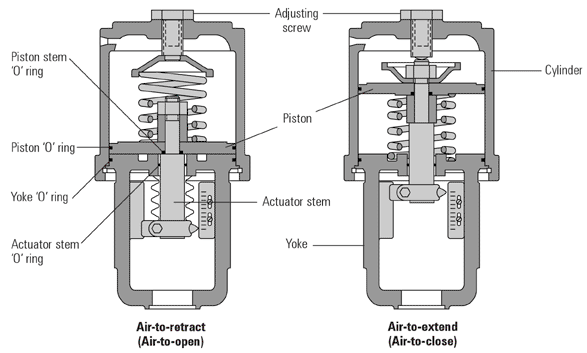
|
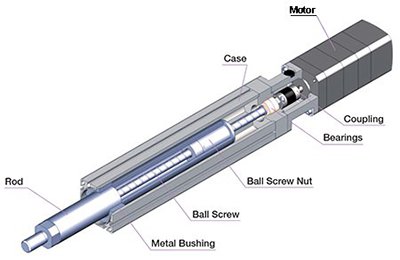
|
Source: https://www.globalspec.com/learnmore/flow_transfer_control/valve_actuators_positioners/pneumatic_valve_actuators Â
|
Source: https://www.orientalmotor.com/linear-actuators/linear-actuators-eac-az-series-absolute-encoder.htmlÂ
|
A pneumatic actuator is also easier and quicker to install due to its simple design. However, its motion profile is more difficult to change after sizing. An electric actuator requires more complicated programming upfront but can easily adjust its motion profile as long as the torque, speed, or load inertia doesn't increase.
Â
TIP: How do They Work? |
Pneumatic actuators consist of a piston inside a hollow cylinder. Their position is controlled by regulating air into the valves, which moves the piston against the spring force. When there's no air pressure, the spring returns the piston to its original position.
Electric actuators convert the rotational force of an electric motor into linear force using mechanisms like a ball screw. By rotating the actuator’s screw with the motor, the ball screw nut moves forward or backward. Positioning is controlled by regulating voltage and current.
|
Â
While the basic design of pneumatic actuators is similar, electric actuators can be driven with several different mechanisms, including ball screws, lead screws, rack and pinion, belt and pulley, etc. These mechanisms alter the final specifications to better suit certain applications.
Â
Here are some examples of different types of electric actuators.
Electric Slide |
Rack and Pinion |
Hollow Rotor |
 |
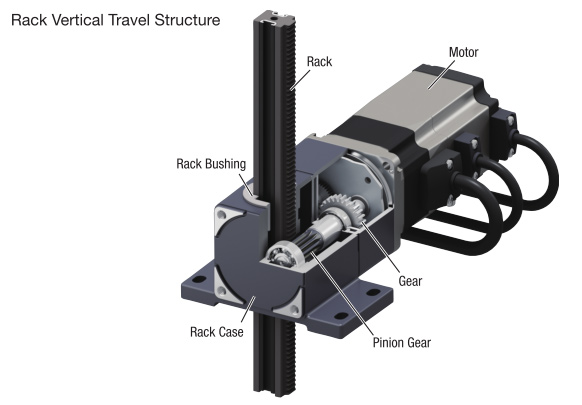 |
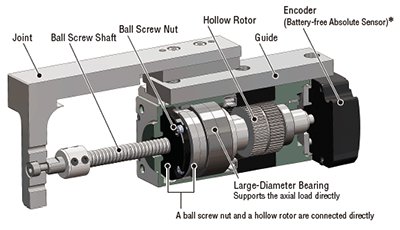 |
Â
There are also different designs for pneumatic actuators, depending on the number of pistons in the cylinder. More pistons mean more force but require more compressed air.
Â
Force & Speed
Traditionally, pneumatic actuators provide higher speeds but lower forces compared to electric actuators. However, factors like screw pitch/lead in electric actuators or the number of pistons in pneumatic actuators can affect this comparison.
For a pneumatic actuator, the force is calculated by multiplying the piston area (force factor) by the air pressure in the cylinder. For an electric actuator, the linear force is converted from the motor's torque.
It's difficult to maintain consistent speed or force with compressed air. Since voltage and current are easier to control, electric actuators can maintain force and speed better without closed-loop feedback. Ball screws or rack and pinion mechanisms on electric actuators also act as gear reduction ratios, so forces can be increased at the expense of speed.
There are many options for electric actuators, so make sure you're comparing apples to apples. Even switching out a ball screw with another ball screw with a higher pitch/lead will alter the final specifications, as shown in the chart below.
Â
The following chart depicts an example of force vs speed for linear actuators.Â
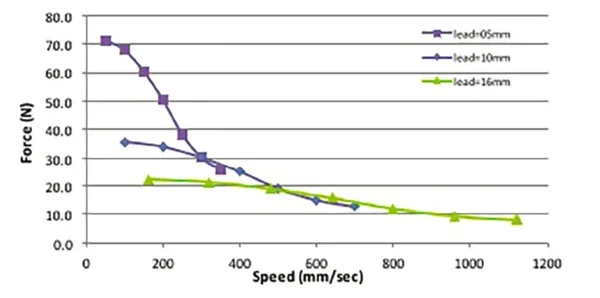
Source: https://www.medicaldesignbriefs.com/component/content/article/mdb/features/articles/26236Â
Â
Pneumatic actuators typically operate from 80 to 100 PSI, and electric actuators convert the motor torque and RPM to a linear force and linear speed. To increase the force or speed of a pneumatic actuator, more pistons and/or air PSI is needed. To increase force or speed or acceleration for an electric actuator, more torque from a bigger or longer motor is needed.
Â
Accuracy & Repeatability
Electric actuators dominate accuracy and repeatability, making them ideal for multi-point positioning applications.
Â
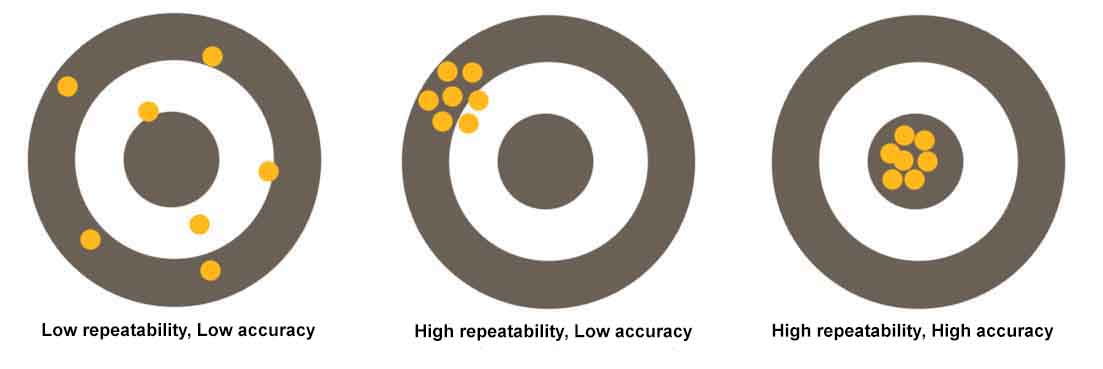
Source: https://www.linearmotiontips.com/does-my-system-need-high-accuracy-or-repeatability-or-both/Â
Â
Since voltage and current are easier to control than air pressure, electric actuators can accurately control their position and repeat that position with the same motion profile. Pneumatic actuators are typically chosen for simple end-to-end positioning applications since they simply cannot achieve the same accuracy and repeatability as electric actuators.
Electric actuators use either servo motors or stepper motors, which already offer high stop accuracy and torque control capability. The holding torque from the motors also prevents position drifting. One thing I noticed is that pneumatic actuators are gradually becoming more advanced as they adopt similar controls as electric actuators, but they would still require additional sensors and programming to achieve close to the "off-the-shelf" accuracy and repeatability of electric actuators while taking up I/O on a PLC.
Â
Motion Control Capability
With more precise control of torque, speed, and acceleration/deceleration patterns, electric actuators can do more with motion profiles than pneumatic actuators.
For example, the following motion profile depicts what an electric actuator or motor can do.
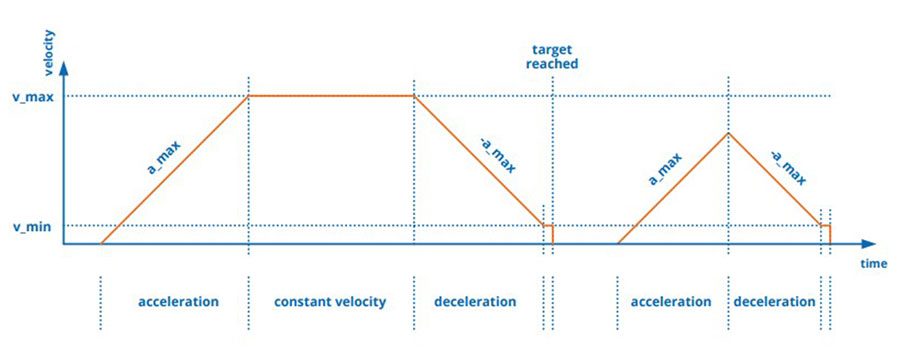
Source: https://www.digikey.com/en/blog/motion-control-profiles-good-better-and-bestÂ
Â
It will be difficult to repeat this exact motion profile with a pneumatic actuator.
Electric actuators are the most capable of repeating specific motion profiles due to their precision and accuracy. Pneumatic actuators are limited in their motion profile generation, and motion profiles are more difficult to change once implemented. For this reason, pneumatic actuators are chosen for single-axis, end-to-end positioning applications. Due to high repeatability, electric actuators are often chosen for multi-point positioning applications and where multiple axes need to be synchronized.
For electric actuators, hundreds of target positions can be saved and stored for multi-point operation. Vibration and shock loads can be minimized with modified motion profiles, such as S-curves, whereas pneumatic actuators need a hard stop and spring.
Â
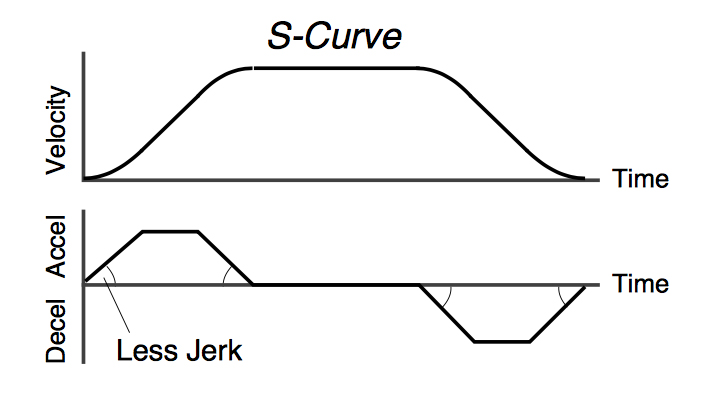
Source: https://www.linearmotiontips.com/how-to-reduce-jerk-in-linear-motion-systems/
Â
Absolute position control has also been advancing for electric actuators for quite some time. For example, in addition to servo motors with absolute encoders, closed-loop stepper motors with built-in multi-turn mechanical absolute encoders can also help minimize footprint by eliminating the external home and limit sensors. The difference is that the mechanical absolute encoder does not need a backup battery like an absolute encoder. Pneumatic actuators have started to offer absolute feedback, but they're not as common.
Â
Efficiency & Cost
Another major benefit of electric actuators is efficiency. Pneumatic actuators operate at about 10~25% efficiency, which is even lower than hydraulic linear actuators at ~40%. Electric actuators operate at around 80% efficiency.Â
Â
Efficiency affects power costs in the long run. Here we compare the energy costs of a pneumatic actuator vs an electric actuator in the same application.
Â
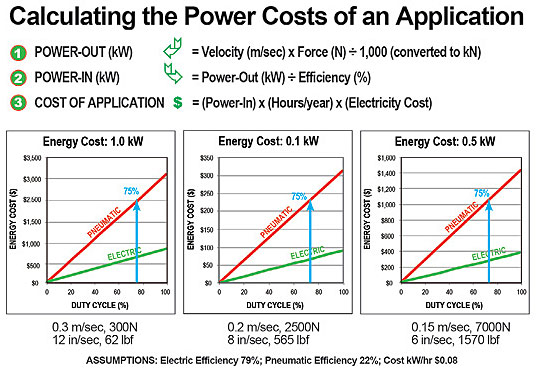
Â
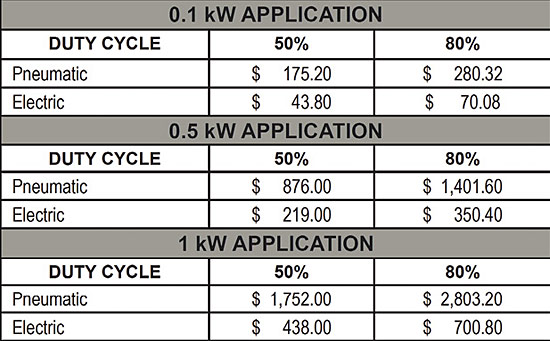
Source: https://www.linearmotiontips.com/electric-actuators-vs-pneumatic-cylinders-total-cost-of-ownership/Â
Â
“Compressed air is one of the most expensive sources of energy in a plant. The overall efficiency of a typical compressed air system can be as low as 10 to 15%.â€â€” U.S. Department of Energy: Energy Tips-Compressed Air, August 2004. |
Knee Brace
Product categories of Knee Brace, we are specialized manufacturers from China, High quality Knee Brace,Protective Knee Brace suppliers/factory, wholesale high-quality products of the Best Knee Brace R & D and manufacturing, we have the perfect after-sales service and technical support. Look forward to your cooperation!
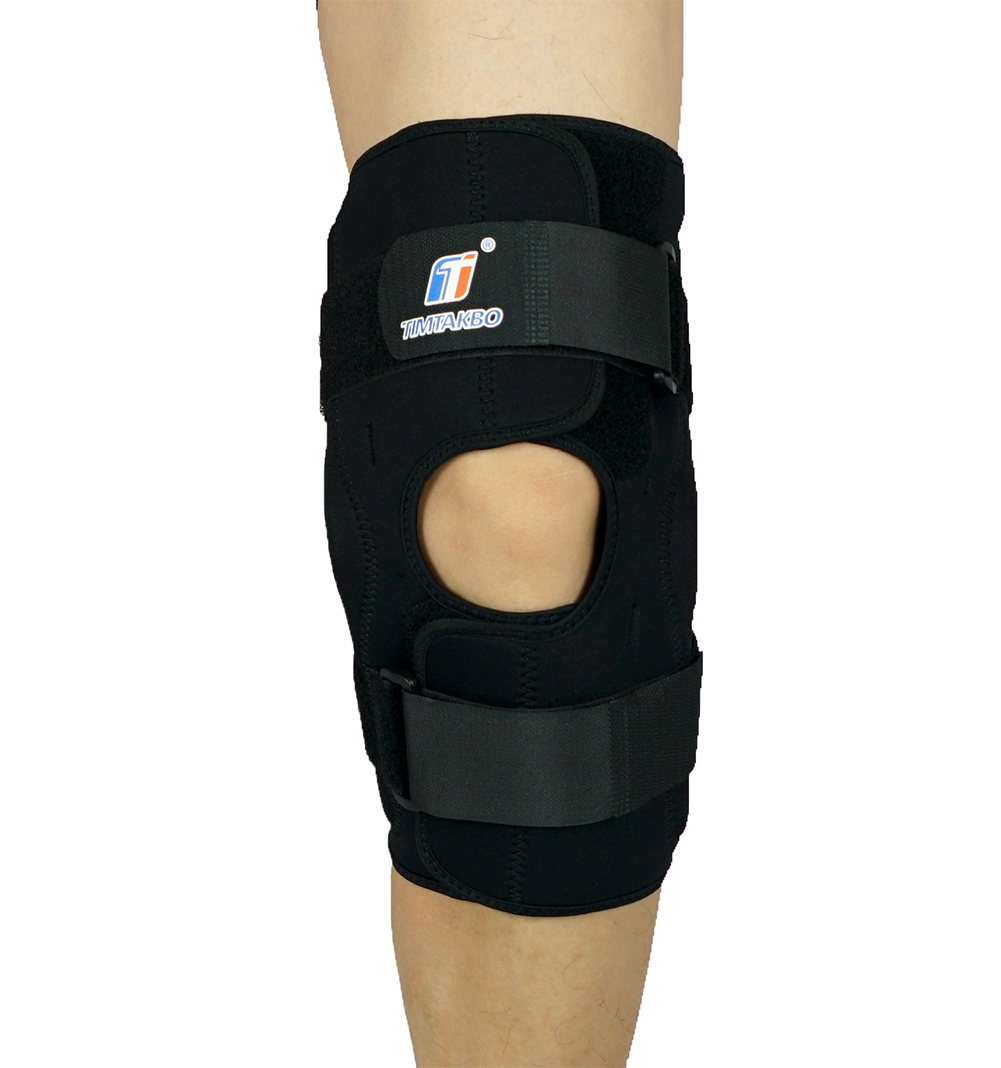
Knee Brace For Knee Pain,Breathable Knee Braces Bupport,Knee Braces For Women And Men
Changsha City Kangbojia Medical Supplies Co., Ltd. , https://www.kbjmedical.com